Статьи/ Богатое семейство углеродных материалов
Богатое семейство углеродных материалов
Ни один элемент Периодической системы Менделеева не обладает тем разнообразием свойств, иногда прямо противоположных,
которое присуще углероду. Столь уникальные свойства - причина того, что и чистый углерод, и содержащие его материалы служат
объектами фундаментальных исследований и применяются в бесчисленных технических процессах. Все это ярко свидетельствует о его
огромной важности для цивилизации.
Страницы: 1 |
2
| 3 |
4 |
5 |
6 |
Пироуглерод
<<...
Пироуглерод - пленки углерода, образующиеся на нагретых поверхностях в результате термодеструкции углеродсодержащих веществ. Процесс образования
пироуглерода можно рассматривать как кристаллизацию из газовой фазы на твердой поверхности (подложке). При t~1700°С получается двухмерно
упорядоченный пироуглерод, при t>1800°C образуется упорядоченный трехмерно пирографит. Размер кристаллита определяется числом зародышей, а
оно тем больше, чем выше температура, соответственно, при более высокой температуре кристаллиты мельче.
В процессе разложения газообразного углеводорода образуются термодинамически устойчивые при этих температурах водород и углерод, как и в
реакции сажеобразования. Экспериментально установлено, что газообразный водород значительно тормозит накопление пироуглерода, поэтому при
достаточно большой длине изделия свойства поверхности пироуглерода на ней могут меняться за счет повышения концентрации Н2 в
реакционной массе. Образование пироуглерода на твердой поверхности происходит одновременно с сажеобразованием, протекающим в объеме газовой
фазы. Эти реакции протекают параллельно и являются конкурирующими. Существует некоторая пороговая концентрация углеводорода (~3-15 об.%), выше
которой выход пироуглерода снижается, и возрастает выход сажи. Значение этой концентрации снижается с уменьшением поверхности отложения
пироуглерода, увеличением времени пребывания реагента и реакционного объема. При нагревании пироуглерода до 2500°С и выше он переходит в
пирографит.
При обсуждении синтеза углерода из газовой фазы речь шла о формировании упорядоченных структур из полностью неструктурированной системы.
Однако при высоких температурах газофазного синтеза процесс формирования кристаллитов проследить практически невозможно. Лучше изучено это
явление на примере жидкофазного синтеза углеродистых тел в связи с тем, что он идет при более низких температурах за более длительное время.
Хотя практически используют тяжелые остатки нефтеперегонки или угле- и нефтепереработки, содержащие высокоуглеродистые соединения, в принципе
не исключено, что возможно образование графитоподобных структур на основе углеводородного сырья легких фракций нефти. В легких фракциях нефти
содержатся преимущественно парафиновые, нафтеновые и моноциклические ароматические углеводороды, в которых атомы С находятся в состоянии
sp2 и sp3-гибридизации. Для перевода этих атомов в состояние преимущественно sp2-гибридизации, характерной
для графита, необходимо проводить дегидроциклизацию углеводородов легких фракций. Этот процесс осуществляют в области термодинамической
стабильности ароматических углеводородов.
В высокотемпературной области термодинамически более устойчивы высококонденсированные арены, состоящие из нескольких ароматических колец и
имеющие общую делокализованную электронную систему. Такие конденсированные ароматические углеводороды можно рассматривать, как зародыши
графитоподобных плоскостей. Коксы c развитой текстурой, образованной крупными кристаллитами, и низкой долей аморфной фазы, при
температуре 1800-2000°С приобретают структуру совершенного графита и называются графитирующимися. Коксы, образованные мелкими кристаллитами
с прочными поперечными связями между ними, и с высокой долей аморфной фазы не приобретают трехмерной упорядоченности даже при 3000°С. Такие
материалы принято считать неграфитирующимися.
Взаимосвязь степени графитации и размеров кристаллита ярко выражена, но не линейна. До степени графитации 0,5-0,6 размер кристаллита
практически не меняется, а затем быстро нарастает. Это значит, что с ростом степени графитации сначала происходит устранение дефектов внутри
кристаллитов без изменения их линейных размеров. После образования графитоподобной структуры пакетов они начинают объединяться в более
обширные формирования, на порядки превышающие свои размеры по сравнению с первоначальными. Такая картина характерна для хорошо графитирующихся
материалов, графитация которых происходит как непрерывное совершенствование и расширение участков графитоподобной структуры за счет практически
полного исчерпания аморфной фазы. Эта разновидность графитации названа гомогенной.
В трудно графитирующихся телах вследствие малых размеров кристаллитов, жестко фиксированных поперечными связями аморфной фазы, не удается
изменить взаимную ориентацию областей упорядоченности с их последующим слиянием. Совершенствование кристаллической решетки происходит только
в границах участков турбостратного углерода почти без увеличения их линейных размеров. Соответственно, значительные количества аморфной фазы
сохраняются в веществе наряду с графитированными кристаллитами даже при температурах порядка 3000°С. Этот вид графитации носит название
гетерогенной.
Таким образом, в интервале температур 2000-3000°С внутри кристаллитов образуется графитоподобная упорядоченность слоев как в
графитирующихся, так и в неграфитирующихся материалах, а доля аморфной фазы снижается до минимума для каждого материала. Как и в случае
карбонизации, различие в их структурах носит количественный характер, и граница между ними размыта. Графитированный материал - искусственный
графит - по своим физическим свойствам и структуре почти не отличается от природных образцов.
Стеклоуглерод
Стеклоуглерод - углеродный материал, отличающийся высокой прочностью, и практически газонепроницаемый. Кроме того, он химически инертен,
особенно в восстановительной атмосфере. Стеклоуглерод хрупок, обладает почти бездефектной внешней поверхностью, чем напоминает неорганическое
стекло. Стеклоуглерод - продукт термической переработки сетчатых полимеров, в первую очередь, фенолформальдегидной смолы, а также целлюлозы. Это
вещества, структура которых не содержит графитоподобных элементов, но включает большое количество связей С-О и изолированных циклов. Первой
стадией получения изделия из стеклоуглерода является формование, а затем отверждение материала при t≤200°C, не связанное с его деструкцией.
В ходе дальнейших превращений форма изделия практически не меняется. При термодеструкции, например, отвержденной фенолформальдегидной смолы
происходят реакции дегидратации с замыканием циклов и значительным снижением содержания кислорода в материале при 300-400°С:
В газообразных продуктах деструкции обнаружены легкие углеводороды, оксид углерода и пары воды. Выше 600°С происходит, по-видимому,
раскрытие фурановых циклов и последующая ароматизация. Рост гексагональных слоев происходит непрерывно с 700 до 3000°С, сопровождаясь реакциями
дегидрирования. Рентгенография стеклоуглерода показывает, что размеры образующихся турбостратных кристаллитов крайне малы, и очень велика доля
аморфного углерода, атомы которого находятся в sp, sp2 и sp3 состояниях. Структура стеклоуглерода представляет собой
клубок беспорядочно переплетенных углеродных лент, состоящих из микрокристаллитов, сшитых углеродными связями различной кратности. Эта структура,
унаследованная от исходного полимера, не поддается графитации даже при 3000°С с длительной выдержкой.
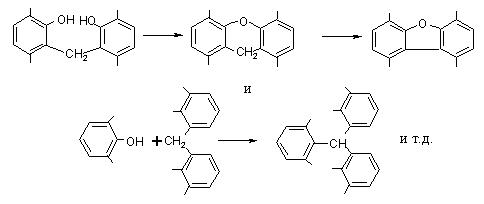
Углеродные волокна
Углеродные волокна первоначально получали по принципам, аналогичным применяемым при синтезе стеклоуглерода. Наиболее распространенным
способом и сейчас является пиролиз и последующая высокотемпературная обработка полимерных волокон. В последнее время разработаны методы
получения углеродных волокон из более дешевого пекового сырья. В обоих случаях волокнистую форму изделию придают на стадии предварительной
обработки, а при пиролизе эта форма уже не изменяется. Волокна из полимерных материалов получают путем выдавливания через отверстия фильеры
с вытяжкой, при этом отдельные структурные элементы полимера, первоначально имеющие, как правило, спиральную или глобулярную форму, приобретают
форму фибрилл - нитевидных образований, длина которых на порядок и более превышает их диаметр.
Следующей стадией является стабилизация волокна, обычно окислительная, сводящаяся к приданию ему неплавкости при последующей обработке.
Понятно, что при этом формирование структуры твердого углеродистого тела происходит в твердой фазе, и возможности ее приближения к идеальной
графитовой ограничиваются, как и в случае стеклоуглерода. Наиболее часто используемое полимерное сырье для получения углеродных волокон -
полиакрилонитрил (ПАН) и гидратцеллюлоза (ГЦ). Основное отличие между ними - наличие кислородных атомов в основной цепи полимера ГЦ. Это
осложняет создание непрерывной ароматизированной структуры карбонизованного материала и, соответственно, последующую графитацию.
В данном случае формирование упорядоченной графитоподобной сетки происходит достаточно легко. Более сложные процессы карбонизации ГЦ-волокна
не позволяют создать однозначную схему последовательных реакций удаления неуглеродных атомов целлюлозы. В общем, из исходной макромолекулы
образуется высокоуглеродистый остаток, сохраняющий форму волокна, и набор газообразных и жидких продуктов деструкции сложного состава.
Карбонизация ПАН- и ГЦ-волокон происходит в интервале температур 400-900°С, графитация - 1800-2500°С. Как и следовало ожидать, лучшая
графитируемость наблюдается у волокон, полученных на основе ПАН.
Пековые волокна бывают двух типов - изотропные и анизотропные. Сырье для анизотропных волокон требует предварительной обработки. Изотропные
волокна при карбонизации и графитации, как и другие изотропные углеграфитовые материалы плохо графитируются. Фибриллы анизотропных волокон
представляют собой вытянутые в длину, хорошо взаимно ориентированные турбостратные слои атомов углерода, образующие вытянутые области. Подобные
структуры создаются при вытягивании волокна из расплава пека. Анизотропные пековые волокна хорошо графитируются, фибриллы графитированного
материала построены из кристаллитов, имеющих структуру графитовой решетки, которые соединены короткими цепочками неупорядоченного углерода.
Последние придают волокну упругость и эластичность наряду с высокой прочностью. Из изложенного следует, что твердофазный синтез углерода из
природных или искусственных полимеров может приводить к структурам, способным или неспособным к графитации. Графитируемость материала при этом
целиком обусловлена строением исходного полимера и степенью упорядоченности его структуры. Как и в случае пековых коксов, после затвердевания
исходного вещества термообработка материала не приводит к образованию обширных областей упорядоченности и развитой текстуры.
Углеродная керамика
Используют также и другую технологию углеродных материалов. Она включает смешение измельченной твердой фазы (наполнителя) с находящимся
в вязкопластичном состоянии связующим, придание получающейся смеси нужной формы и последующую термообработку. В качестве наполнителей
применяют достаточно большой набор твердых углеродистых веществ: каменноугольные, нефтяные и сланцевые коксы, термообработанный антрацит,
сажу и т.д. Выбор связующего намного более ограничен, это, как правило, нефтяные и каменноугольные пеки. В композиции наполнитель-связующее
применяется твердая фаза, уже прошедшая стадию карбонизации. В связи с этим процесс получения углеродного материала на ее основе есть процесс
карбонизации связующего в присутствии порошка наполнителя.
Опыт показывает, что для получения прочного материала необходимо наличие лиофильных (смачиваемых) и лиофобных (несмачиваемых) участков
поверхности частиц наполнителя. Лиофильные участки обеспечивают контакт поверхности со связующим, лиофобные - взаимный контакт твердых
частиц. Соотношение смачиваемых и несмачиваемых поверхностей должно быть близко к 0,3-0,5, но может изменяться для конкретного материала.
Как лиофильность, так и лиофобность поверхности могут быть изменены при ее обработке растворителями, газообразными реагентами или в
результате термообработки.
Практически прочность получающихся искусственных графитов ограничена прочностью графитированного кокса из связующего. Она, как правило,
определяется долей пор в материале кокса. Плотность его оказывается ниже, чем у природного графита, в основном, за счет образования пор
при выделении летучих веществ и усадке материала. Отчасти влияние эффекта порообразования может быть устранено за счет пропитки
карбонизованного материала, например, низковязким пеком с последующим обжигом. Такой процесс повторяется до достижения постоянной
массы изделия. Более эффективно уплотнение пироуглеродом, осаждающимся из газовой фазы. Это позволяет повысить плотность и прочность
материала, но не дает возможности улучшить собственно кристаллическую структуру искусственного графита до почти идеальной гексагональной
упаковки естественного.
Эту задачу удалось решить, используя явление ползучести графита под действием механической нагрузки при высоких температурах (метод
термомеханической обработки - ТМО). Добавки металлов-катализаторов (карбидообразователей) позволили ускорить процесс совершенствования
структуры графита под давлением. Этот способ графитации был назван термомеханохимической обработкой (ТМХО). Продукт графитации под
давлением получил название рекристаллизованного графита. Уплотнение материала за счет ползучести происходит благодаря пластической
деформации отдельных элементов углеродного тела без нарушения его сплошности.
... Продолжение статьи>>
Авторы статьи: А.Дунаев, А.Шапорев
Источник: Нанометр
Страницы: 1 |
2
| 3 |
4 |
5 |
6 |
Перейти к разделу "Статьи"
|